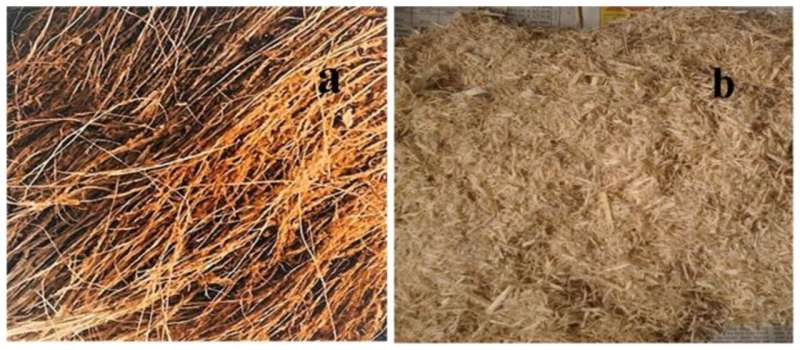
An international team of scientists is helping to reduce carbon emissions into the atmosphere by exploring different natural fibers and blending the natural fibers in plastics to make light-weight and strong green composite materials for the construction and automotive industries.
Bagasse fibers are the fibrous residue that remains after sugarcane stalks are crushed to extract the juice. They are a byproduct of the sugarcane industry but they can also be used to make paper, packaging materials, and biodegradable plastics, textiles and polymer composite materials, all in the name of sustainability and as eco-friendly alternatives to traditional materials.
Coconut husk fibers, also known as coir fibers, are the fibrous material found between the hard, internal shell and the outer coat of a coconut. These fibers are strong, durable, and resistant to saltwater, making them ideal for a wide range of applications. Coconut husk fibers are commonly used for making rope, twine, doormats, brushes, and various other household and agricultural products. Like bagasse fibers, coconut husk fibers can be a low cost sustainable alternative to synthetic fibers in the production of natural fiber-reinforced polymer composites for various applications.
Recently, Verma Deepak, from Graphic Era Hill University (India), and his team of international researchers, have developed a method using a blend of coconut husk (COIR) and bagasse fibers, together with calcium carbonate, for reinforcing epoxy composite materials. The novel part of this method is the treatment of the fibers with a chemical to make the composite stronger and less likely to absorb water, thus enhancing the mechanical and thermal properties of the fibers.
Upon evaluating the bagasse/COIR reinforced epoxy composite material for its mechanical strength and structure when exposed to high temperatures, Verma and his team found that the treated composite was much stronger and could handle more weight compared to untreated natural fibers reinforcing the resin composite. The treated fiber reinforced composite also provides for enhanced heat resistance to failure under high temperature. The findings from the study have been published in Sustainability.
The novel method was the results of several years of experimentation as part of the team’s key mission to solve the natural fiber problem of tendency to absorb moisture and degrade quickly. Verma and his team became interested in this area when they were reviewing the literature on the hydrophilicity of natural fibers, which makes the mechanical properties of the composite materials low.
From the literature, they learned that to improve the adhesion of these materials to the matrix, the fibers need to be treated chemically or physically to increase their hydrophobicity. They published the review of the hydrophilicity topic in 2020 in the Journal of Natural Fibers, with a focus on on how to improve the mechanical properties of polymer-based composite materials by treating the surfaces of natural fibers and natural particles.
The review paper discussed the physical properties of these materials, the different chemical treatments available, how to process them, and the mechanical properties of the composite materials. Verma and his team then set out to develop a novel method to improve the natural fiber mechanical properties and overcome the hydrophilicity limitation by treating the fibers with chemicals like alkalization/mercerization. That study was reported in the Journal of Composites Science in 2021.
Importantly, Verma and his team also managed to form a community of researchers with a focused mission: to collaborate to study the wider implications of the hydrophilicity problem in natural fibers. The knowledge of this subject has been published in an edited book (Verma, 2021).
More information:
Deepak Verma et al, Thermomechanical Analyses of Alkali-Treated Coconut Husk-Bagasse Fiber-Calcium Carbonate Hybrid Composites, Sustainability (2023). DOI: 10.3390/su15021686
Provided by
Newcastle University in Singapore
Citation:
Reinforced polymer hybrid composites for low carbon applications in the construction and automotive industries (2023, April 3)
retrieved 3 April 2023
from https://techxplore.com/news/2023-04-polymer-hybrid-composites-carbon-applications.html
This document is subject to copyright. Apart from any fair dealing for the purpose of private study or research, no
part may be reproduced without the written permission. The content is provided for information purposes only.
Stay connected with us on social media platform for instant update click here to join our Twitter, & Facebook
We are now on Telegram. Click here to join our channel (@TechiUpdate) and stay updated with the latest Technology headlines.
For all the latest Technology News Click Here
For the latest news and updates, follow us on Google News.