One sunny morning last month, an earthquake jolted northeast San Diego. Minutes later, another temblor hit, causing a 10-story wood building to sway.
The quakes, though, were triggered by a computer and the shaking was confined to a 1 000-square-foot platform on which the building — a full-size test model — stood.
The structure is the tallest ever subjected to simulated earthquakes on the world’s largest high-performance “shake table,” which uses hydraulic actuators to thrust the steel platform through six degrees of motion to replicate seismic force. The shake-table trials at a University of California at San Diego facility are part of the TallWood Project, an initiative to test the seismic resiliency of high-rise buildings made of mass timber. An engineered wood building material, mass timber is increasingly popular as a more sustainable alternative to carbon-intensive concrete and steel.
The mockup has been already subjected to more than 100 seismic events during the $3.7 million experiment, and will undergo more before the testing period ends in August.
“You’re putting a building through the number of quakes it will never, ever experience unless it’s around for 5,000 years,” says Thomas Robinson, founding principal of Lever Architecture, a Portland, Oregon, firm that helped design the TallWood structure.
Recent changes to buildings codes in the US permit mass timber buildings as tall as 18 stories. But unknown until now is how such high-rises would fare in earthquake-prone areas of the world like California.
On the first day of testing in May, anticipation runs through a crowd of hard-hatted architects, engineers and researchers as they gather a safe distance from the building, which stands on the shake table like a deconstructed rocket ready for liftoff. A bank of video cameras is pointed at the structure and a drone buzzes overhead.
The first three stories of the 112-foot-high building are clad in silver and orange panels that frame glass windows. The rest of the building is open-air, with each floor containing four “rocking walls” engineered to minimize structural damage from earthquakes. Engineers also built interior walls and staircases designed to survive severe shaking and installed sensors throughout the building.
Two five-story, rust-coloured metal “protection towers” flank the building on one side and cables tether it to the ground on the opposite side to break its fall if the structure collapses during testing.
This morning, engineers have programmed the shake table to reproduce two devastating earthquakes. The first is the 6.7-magnitude Northridge quake that struck Los Angeles in 1994 and that, in 20 seconds, caused more than $40 billion in damages as buildings and freeways collapsed, killing 60 people. More than 2,400 people lost their lives in the second disaster, the 7.7-magnitude Chi Chi quake that hit Taiwan in 1999 and crumbled concrete-and-steel high-rise buildings.
Loudspeakers broadcast the countdown to the first quake: “Northridge. 3D motion. Northridge 3D motion. Five, four, three, two, one.” The building begins to sway from side to side, creaking and groaning during the minute-long simulation. Applause erupts as mission control announces “Northridge complete” and the building comes to a rest.
Six minutes later another countdown begins. The far more powerful Chi Chi quake simulation shakes the building from side to side and to and fro. The tests lasts for a minute, twice as long as the actual quake that left 100,000 people homeless and ranks as the most powerful temblor to strike Taiwan in the 20th century. It is the type of catastrophic quake that Californians call “the Big One.”
After a half hour, inspectors deem the building safe to enter. On the third floor, Shiling Pei, the TallWood Project’s principal investigator, examines the walls and floor. “This is exactly the results that we’re looking for, which is no structural damage,” says Pei, an associate professor of civil and environmental engineering at the Colorado School of Mines. “That means the building could be reoccupied quickly.”
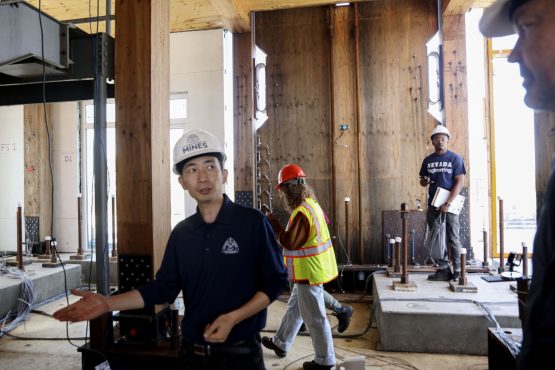
SAN DIEGO CA-MAY 9: Structural elements inside a building after an earthquake simulation byengineers from the University of California San Diego and several other universities in San Diego, California on Tuesday, May 9, 2023. Image: Sandy Huffaker/Bloomberg
Avoiding expensive structural repairs and putting buildings swiftly back into service reduces an earthquake’s economic and social impacts, according to Robinson, who noted that the exterior walls of the TallWood building remained in alignment despite the intense shaking. “It’s usually right where the corners meet where you get vast damage,” he says.
The fact that there was minimal impact to nonstructural parts of the building, such as staircases and facades, is also significant, according to Pei. “You see the nonstructural system opened up a little bit,” he says, pointing to an interior wall. “But repairing that will not be that costly, just patching drywall.”
The researchers are testing four different building facade assembles. Three are drywall-covered steel frames with aluminium composite panels as the exterior finish, each secured to the building in a different way. The fourth facade is a glass curtain wall. One of the aluminium panels popped out during the seismic tests, but the facades all remained attached to the building.
The TallWood building’s ability to withstand back-to-back simulated earthquakes speaks to the natural flexibility of wood construction and the architectural systems designed to strengthen the structure, such as the rocking walls. The north-south rocking walls are constructed from mass plywood panels made from spruce, pine and fir while the east-west walls are Douglas fir cross-laminated timber. Steel rods anchor the walls to the foundation. When an earthquake strikes, the walls rock back and forth to dissipate seismic energy and when the shaking stops, the steel rods pull the building back to center.
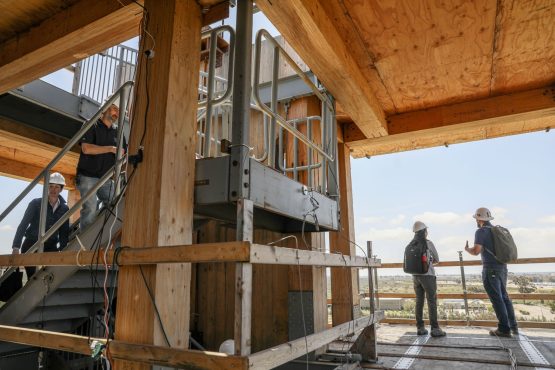
SAN DIEGO CA-MAY 9: Structural Engineers look over the inside of a buildingtafter an earthquake simulation in San Diego, California on Tuesday, May 9, 2023. Image: Sandy Huffaker/Bloomberg
Much of the mass timber in the structure came from Boise Cascade Co. tree plantations in Oregon. “With recent building code changes, we see this as just a great market to be in,” says Daniel Cheney, director of engineering at the wood products company. “Up to that point, it was still concrete for commercial buildings. Now there’s a lot more opportunities.”
Just don’t expect to see supertall mass timber buildings. Pei and Robinson say that above 18 stories, a mass timber structure lacks the stiffness to withstand winds that buffet high towers.
TallWood (officially, the Natural Hazards Engineering Research Infrastructure TallWood Project) is run by a consortium of universities and has received funding from the National Science Foundation and US Forest Service as well as private building-industry companies.
When the quake trials are completed, the structure will be dismantled and parts of it recycled to construct other test buildings. The researchers anticipate the results of the shake tests will spur construction of more high-rise mass timber buildings by assuring architects, builders and government officials of their durability.
“I think mass timber is a great solution for sustainability, for economics,” says Keri Ryan, an engineering professor at the University of Nevada, Reno, who led the team that developed the nonstructural parts of the TallWood building. “So I hope that this really helps get people excited that we’ve got a resilient mass timber system that works.”
© 2023 Bloomberg
Stay connected with us on social media platform for instant update click here to join our Twitter, & Facebook
We are now on Telegram. Click here to join our channel (@TechiUpdate) and stay updated with the latest Technology headlines.
For all the latest Business News Click Here
For the latest news and updates, follow us on Google News.