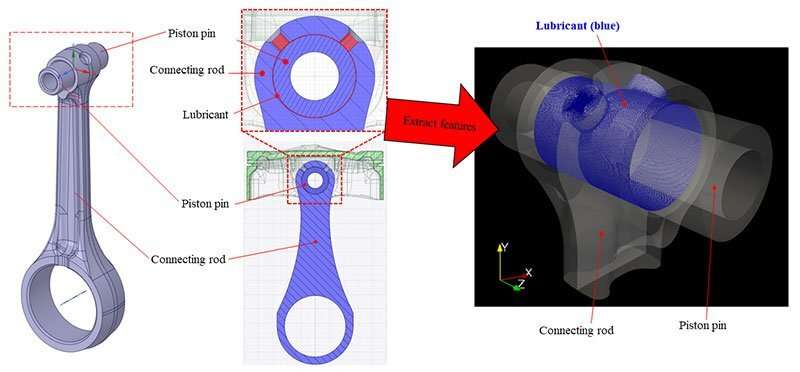
A research group has created an analysis method to predict wear and seizure locations in the sliding parts of engine piston pins. The breakthrough will help limit wear and tear on transportation and industrial machinery components and make them more fuel efficient.
Details of their discovery were published in the Journal of Tribology.
Improvements to the efficiency of internal combustion engines are necessary if we are to overcome their environmental and sustainability problems. Reciprocating engines use reciprocating pistons to extract power from combustion and convert it into rotational motion. They are commonly used in automobiles.
The most common cause of reciprocating engine failure occurs when the oil film of the lubricating oil breaks, causing metal parts to come into contact, resulting in scratching and sticking. When such a seizure happens, it is impossible to start the engine.
Piston pins and connecting rods in constant reciprocating and rotating motion require fluid lubrication. However, long-term loading tests are needed to verify the wear and seizure locations in fluid lubrication, and predicting or calculating this was thought to be unattainable.
That was until Professor Jun Ishimoto led a group at Tohoku University’s Institute of Fluid Science and Honda Motor Co., Ltd. that established the multiphase fluid-structure coupled analysis method. It not only simulated and predicted tribological properties under severe loading conditions but also identified the piston pin’s bow-like defamation as the cause of mechanical contact and seizure at the connecting rod edge.
“Proper safety guidelines that help prevent unnecessary damage to automobile engines and other industrial machinery will be easier to create thanks to this prediction method,” said Ishimoto.
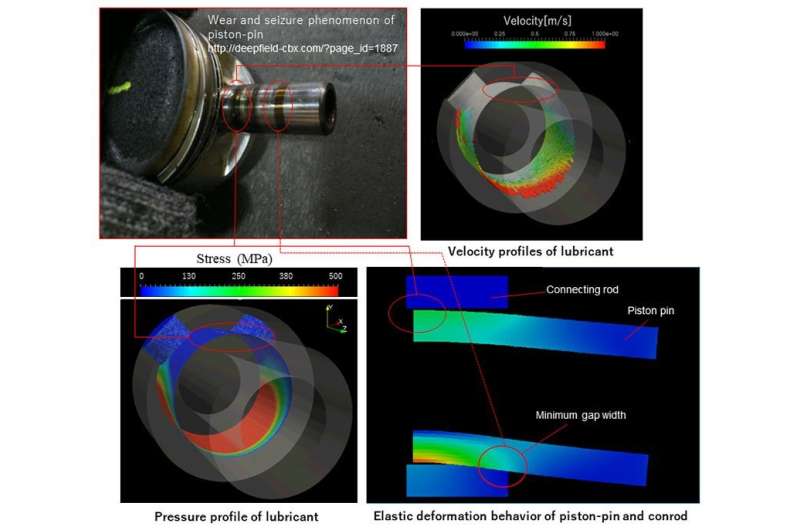
Yudai Narumi et al, Computational Fluid–Structure Interaction Analysis of Piston Pin Multiphase Elastohydrodynamic Lubrication with Unsteady Flow Channel Variation, Journal of Tribology (2022). DOI: 10.1115/1.4055407
Citation:
Computationally predicting where wear will occur in engines (2022, October 5)
retrieved 5 October 2022
from https://techxplore.com/news/2022-10-computationally.html
This document is subject to copyright. Apart from any fair dealing for the purpose of private study or research, no
part may be reproduced without the written permission. The content is provided for information purposes only.
Stay connected with us on social media platform for instant update click here to join our Twitter, & Facebook
We are now on Telegram. Click here to join our channel (@TechiUpdate) and stay updated with the latest Technology headlines.
For all the latest Technology News Click Here
For the latest news and updates, follow us on Google News.